Por Adriana Romero, Christopher Feldmann, Katherine Silva, José Barros, Gustavo Martínez, Marcelo Montero, Juan Álvarez y Eugenio Ferrigno (Y-TEC)
Para identificar tempranamente eventos anómalos en pozos con sistema de extracción plunger lift , y así evitar pérdidas de producción y aportar opciones de mejoras, se desarrolló una herramienta de diagnóstico usando ciencia de datos e inteligencia artificial
El sistema de extracción plunger lift permite el levantamiento de líquidos tanto en pozos de gas como de petróleo. Este sistema de extracción es actualmente uno de los más utilizados en los yacimientos de petróleo y gas no convencionales (NOC Oil y NOC Gas) operados por la empresa argentina YPF S.A., representando el 49% (300 pozos) y el 40% (100 pozos) del total de los pozos respectivamente.
En particular, en el caso de los pozos con Plunger Lift, la presión de cabeza presenta un patrón de comportamiento con características muy particulares, con lo es posible identificar cualquier tipo de anomalía o fallo en su funcionamiento.
Para encontrar tales fallas, los ingenieros de producción deben recorrer cada una de las gráficas de la presión de cabeza y así saber si el pozo está fallando. Después se revisa la configuración del controlador del pozo y otras variables lo que le permite identificar el problema y tomar una decisión para corregirlo.
Debido a que el número de pozos es alto y los recursos tanto en tiempo como en personas es limitado, algunos pozos pasan un tiempo considerable fallando sin ser revisados, lo que implica una pérdida de producción significativa.
Para identificar estos eventos de manera temprana evitando pérdidas de producción y generando oportunidades de optimización es que se desarrolló una herramienta de diagnóstico usando ciencia de datos e inteligencia artificial.
Antecedentes
La Figura 1 muestra la tendencia de la presión de la cabeza, la presión de la casing y el estado del pistón.
El sistema plunger lift funciona en un proceso cíclico, es decir, el pozo fluye y se cierra alternadamente. Durante el período de cierre mientras el pistón está en el fondo, la presión del gas aumenta, y cuando aumenta lo suficiente, la válvula del motor se abre para permitir que el pozo fluya. El gas en el espacio anular se expande en el tubo, elevando el pistón y los líquidos a la superficie, con algo de ayuda del gas que se produce. Se permite que el yacimiento produzca gas hasta que el nivel de producción descienda hasta un nivel casi crítico ya si se deja fluir más tiempo el pozo puede ahogarse.
Entonces el pozo se cierra, y el pistón cae de nuevo al resorte de amortiguación, primero a través del gas y luego a través del líquido acumulado, durante el cierre hay un período de aumento de la presión. Entonces el ciclo se repite.
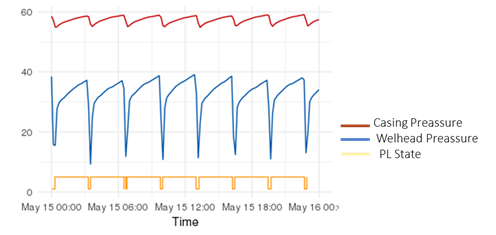
Figura 1 - Variables de análisis en un pozo con plunger lift
- Desarrollo técnico del trabajo
Para definir las acciones de optimización, primero es necesario conocer los tipos de fallos que existen. Para ello se analizan variables como el arribo del pistón, la velocidad del mismo, los ciclos realizados, la producción, entre otros. Para diagnosticar un pozo con plunger lift, se toma en cuenta la velocidad de arribo del pistón como la principal variable de este estudio, ya que esta variable permite identificar si el pozo está funcionando correctamente (está optimizado) o si requiere alguna acción de mejora. Sin embargo, hay pozos que no tienen datos de telemetría de esta variable. En esos casos, el diagnóstico se realiza analizando la presión de la cabeza del pozo. Algunos de estos diagnósticos se consideran de mayor importancia ya que representan pérdidas de producción, mientras que otros pueden indicar una desviación operativa y/o una oportunidad de optimización.
A continuación, se listan los diagnósticos que el algoritmo clasifica.
- Pozo abierto/cerrado: Se dice que un pozo está abierto o cerrado cuando su ciclo normal de apertura y cierre se interrumpe por algún fallo que impide que el controlador del pozo funcione correctamente. Este tipo de fallo constituye una pérdida de producción.
- 100% de arribos: Se refiere a aquellos pozos en los que, durante un período de estudio de 24 horas, en la mayoría de sus aberturas llegó el pistón. Sin embargo, este diagnóstico puede subdividirse según su velocidad de llegada, ya que, según los estudios realizados, se considera que la velocidad óptima de llegada del pistón debe estar entre 220 m/min y 300 m/min. Teniendo en cuenta lo anterior, este diagnóstico se subdivide de la siguiente manera:
- Optimizada: corresponde a aquellos pozos en los que la mayoría de las llegadas en 24 horas están dentro de la ventana óptima.
- 100% de arribos (velocidad del pistón fuera de rango): corresponde a aquellos pozos que tienen 100% de arribos, pero su velocidad está fuera de la ventana óptima. Este diagnóstico representa una oportunidad de optimización.
- 100% de arribos (velocidad crítica): corresponde a aquellos pozos en los que se calcula que la velocidad de llegada es superior a 500 m/min. Este diagnóstico es de gran impacto, ya que, debido a su excesiva velocidad, se puede generar una rotura de pistón y/o de la instalación.
- Arribos intermitentes: Se refiere a aquellos pozos en los que el porcentaje de llegadas es inferior al 80%.
- Comprobar el sistema de extracción/comunicación: Este diagnóstico corresponde a aquellos pozos que presentan una interrupción de comunicación o que las variables no fueron censadas correctamente.
- Sin arribos: Este diagnóstico corresponde a los pozos en los que no se registra el arribo del pistón, por lo cual es imposible diagnosticar el tipo de falla.
Metodología
La conceptualización de esta propuesta comenzó definiendo los diferentes tipos de pautas de producción en los pozos plunger lift que podrían dar lugar a pérdidas de producción o a posibles oportunidades de optimización de la producción. Según la instrumentación del pozo se utilizó un enfoque diferente.
Los pozos con sensor de arribo se diagnosticaron utilizando la experiencia de los ingenieros de producción. En los pozos sin sensor de arribo, se utilizaron técnicas de series temporales para comparar y aislar las pautas de producción típicas disponibles en los datos históricos sobre la presión en la cabeza del pozo. Este patrón se convirtió posteriormente en imágenes y esas imágenes se clasificaron utilizando redes neuronales.
Diagnóstico según el estado de las variables para los pozos con detección de arribo
Un sistema plunger lift es operado por un controlador, el cual es reactivo respondiendo al estado del pozo.
El controlador esperará a que el émbolo caiga basándose en un parámetro introducido por el usuario. El sistema entonces esperará a que la válvula se abra hasta que se cumplan todas las condiciones, ya sea de tiempo o de presión.
El estado de "Llegada del pistón" se basa en los valores determinados por el usuario para la llegada esperada en función de la profundidad y la carga de fluido. Si el émbolo no llega como se espera, entonces se dice que el pozo necesita ser optimizado, ajustando los parámetros que mejorarán los ciclos futuros. Para este tipo de pozo se establecieron las reglas de diagnóstico, según el estado de las variables, se etiquetan los casos según los cinco listados en el punto anterior y el diagnostico se entrega al usuario.
Diagnóstico basado en la red neuronal
Para la clasificación utilizando la red neuronal, primero, la serie temporal se transforma en una imagen usando gráficos de recurrencia (ver Figura 2), para luego realizar una clasificación utilizando las redes neuronales.
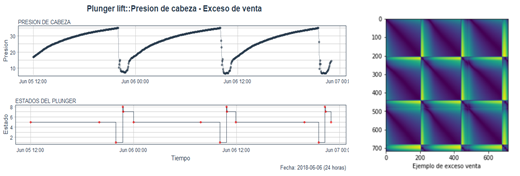
Figura 2 Transformación de serie de tiempo a gráfico de recurrencia
Se etiquetaron imágenes con los casos a clasificar: aquellos pozos en los que la periodicidad es regular en el tiempo, etiquetados como llegada normal de pistón; y aquellos pozos en los que la periodicidad es irregular, etiquetados como llegada errática de pistón, pozos abiertos y pozos cerrados. Con estos ejemplos se realizó el entrenamiento del clasificador, utilizando redes neuronales.
Una vez implementada la herramienta se mejoraron los criterios de análisis y por tanto la eficiencia obtenida, alcanzando valores del 94% para el NOC GAS y del 80% para el NOC OIL.
Los diagnósticos entregados por el algoritmo se encuentran actualmente en los tableros de manejo por excepción en los espacios colaborativos de NOC Oil y NOC Gas. Adicionalmente se proporciona un informe con la lista de los pozos que tienen algún tipo de evento evitando así perder el tiempo analizando todos los pozos, y atendiendo en cambio como prioridad a aquellos que realmente lo requieren.
Entre las mejoras, tanto operacionales como económicas, consideradas con el desarrollo del algoritmo, cabe destacar las siguientes:
- Reducción del uso del equipo de Slick Line. Un pozo optimizado no permite la acumulación de parafina.
- Se optimizó el manejo de eventos anormales, centrándose en las cuestiones más relevantes, ya sea por producción o por operación.
- Se logró una mejor distribución de los recursos sobre el terreno (recorredores/operadores de campo) en conjunto con ingeniería de producción, siendo más eficaz la programación.
- Reducción de las desviaciones operacionales y mejora de las condiciones de los pozos.
- Aumento de la producción.
- El presente trabajo describe el desarrollo y la aplicación de un software de clasificación de fallos para pozos de petróleo y gas con sistemas de extracción plunger lift. El software implementado se utiliza para gestionar eventos anormales por excepción.
- La herramienta tiene una eficiencia de detección de fallos del 94% para los pozos de gas y del 80% para los pozos de un total de aproximadamente 400 pozos productores que utilizan el sistema plunger lift.
- El uso del software desarrollado ha producido mejoras tanto económicas como operacionales. Se logró un aumento de la producción gracias a la pronta identificación de los pozos defectuosos. Además, la utilización del algoritmo mejoró considerablemente el tiempo de detección de las fallas, asegurando una mejor gestión de los recursos destinados a la optimización del equipo de elevación del émbolo.
- El algoritmo funciona actualmente en 400 pozos de Loma Campana y se está evaluando su extensión a otros campos de YPF.
- El software se encuentra actualmente en un proceso de mejora para aumentar la eficiencia del diagnóstico de los pozos con sensor abierto/cerrado y sin arribo.
|